Silage Sheet Seam
There is a new product called Silage Sheet Seam that has been developed (2021) for use with silage sheets on farms. It is designed to be an improved version of the old Strip-seal that was available in the 1960’s and 1970’s. Sheet Seam is designed to secure the edges of silage sheets to form an airtight seal and strong join between sheets. It should be capable of allowing vacuum extraction of silage clamps. It should also improve the seal where sheet edges meet on clamps that do not use vacuum extraction. It can be used in settings other than farms where plastic sheets need to be sealed and joined.
The basic idea is to clip edges of sheets together using a tube and channel system. The tube is placed on top of the sheets, and the channel below the sheets, and then the tube is pressed into the channel trapping the sheet edges between the tube and the channel by compression. The precision fit should produce a seal of about 24 mm width of the sheets clipped into the channel. Sheet Seam is designed to work with silage sheets of thickness 75 micron to 150 micron. (Micron=micrometre=mu=mi=μm) Visqueen Agri-S sheets are in this range at 125 micron thickness.
This product is experimental with no guarantees for the year 2022 (statutory customer rights still apply). Some tests have been applied to small bales pods and so far Sheet Seam has performed at least as well as the old Strip-Seal product. The improvements that have been made include a more precisely engineered channel, greater channel flexibility, a tighter fit of the tube, UV stabilisation, modern plastic materials, a more flexible and more visible colour tube (Zinc Yellow). Sheet Seam is now available in 100 m lengths, coiled for transport diameter less than 1.2 m. A limited run of 30 coils of 100 m has being produced for the first year (2022).
Unlike heat sealing or glue/sealant sealing, Sheet Seam sealing is reversible. Sheets can be sealed and unsealed using Sheet Seam as often as required.
Samples are available. Some images have been uploaded below. More will follow showing how to use it.
A small stock exists in Devon, UK. Anybody interested in having a sample can get details from the following email address. There is no other website serving this small company. It is run through this email address only.
CDavidLanceSilage@gmail.com
The cost of 100 m rolls and 50 m rolls of Silage Sheet Seam can be given on request. Rolls will only be sold to customers that have evaluated samples for themselves before ordering. As of 1st May 2022 rolls of Silage Sheet Seam are now in stock and available for sale.
Back to home page Yalland Vacuum Compressed Silage
Pressure testing of Sheet Seam has been conducted. A video exists but it is nolonger available online.
Silage Sheet Seam Diagram
Silage Sheet Seam (Cross Section New October 2021)
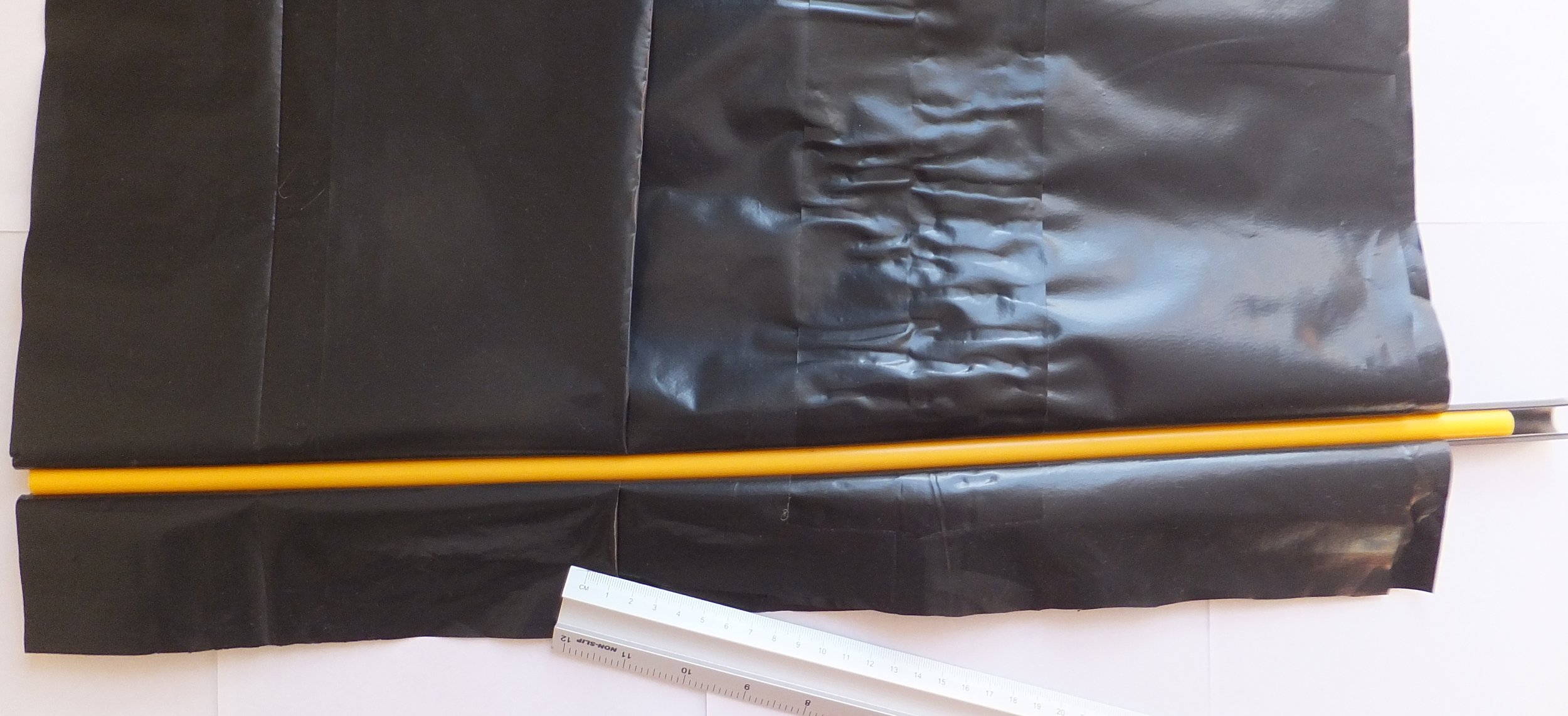
New Silage Sheet Seam sample
Part roll of Silage Sheet Seam with Visqueen Silage Sheets
Previous Advertisement in the Farmers Weekly
Silage Sheet Seam
(Standard issue text with samples and rolls of Sheet Seam)
Sheet Seam for plastic silage sheets is a channel and tube clipping system that can be used to join or seal plastic sheets together. Suitable for sheets of thickness in the range of 75 micron to 150 micron.
Based on a system that was available in the 1960’s and 1970’s called “Strip-seal”, this product has been redesigned and made using the latest plastic extrusion technology. The material is MDPE (Medium Density Poly Ethylene, also known as Alkathene).
Improvements on the old Strip-seal product include UV protection, more precise tube fit in the channel, more visible inner tube and the latest standards in plastics extrusion.
This product is new in 2021 and is regarded as experimental for the first season as farmers test the product on the farms. The quality of the plastic is guaranteed by the manufacturer but the effectiveness of the product in joining and sealing silage sheets is yet to be confirmed.
The old Strip-seal product was developed in the 1960’s for use in the Vacuum Compressed Silage method. That method does not appear to be used at the moment, but the issue of effectively sheeting down silage clamps is always under development and this product may help with that.
It is hoped that Sheet Seam will enable farmers to use Vacuum Compression in silage making, or at least seal clamps more effectively than before. That should enable farmers to make better quality silage.
It is hoped that Sheet Seam will prove to be an investment rather than a disposable item. If used with care and conservation, Sheet Seam should last last for many years. Samples of the old Strip-seal are still usable after more than 40 years. It remains to be seen how long Sheet Seam lasts.
Feed back on this product can be given on The Farming Forum using the Vacuum Silage thread on the Livestock & Forage Forum.
Guidance on using Sheet Seam
New rolls should be fully unwound, by rolling out on grass, and checked for any damage. It may be useful to uncouple and then couple up some, or all, of the roll of Sheet Seam to get used to the force and technique required, before using it with sheets. Care should be taken to avoid kinks.
1. Look after your Sheet Seam by keeping it away from anything that might crush, cut or abrade it. Clean by rubbing with a handful of grass before and after use. Also clear and clean the surfaces of sheets that are going into the channel using handfuls of grass.
2. Plan for where the clamp needs to be opened for letting gas out and for when the silage needs to be opened for feeding. The ends of the Sheet Seam need to be in that opening position.
3. Ensure sheets are under control using weights before sealing with Sheet Seam.
4. Align sheets as required over the channel and press the tube and sheets into the channel to trap the sheets. Ensure the tube fully “clicks” into the channel.
5. When one sheet is longer than the other, plan ahead before getting to a corner and take in overlaps in the longer sheet (like pleats). Do not allow more than three thicknesses of the longer sheet to develop. Lie each pleat over the sheet and press all three layers onto the other sheet and into the channel using the tube.
If the corners don’t meet then release sheets back to a point where there is enough distance before the corner to lose the excess length in overlaps without creating more than three layers of the longer sheet in the channel. Excess layers of sheet in the channel may compromise the seal and may stretch or break the channel. It is also very difficult to work with. Maximum of four layers in the channel made up of one short sheet + up to 3 long sheet layers.
6. Joins in the Sheet Seam can be made by using all of the first length up on the sheets, then lying the next length next to the first with at least a 2 foot overlap. Then press the sheets into the new length in a position as close to the first as possible until beyond the end of the first length.
7. Opening Sheet Seam is best done at an end. Sheets may be damaged by attempting to open the seam anywhere else.
8. The MDPE Sheet Seam materials are stable between -40 C and 100 C. They are also resistant to UV in sunlight and acid conditions down to pH 3.5. The materials will last longer if they are cleaned and put under cover when not in use. The channel is stronger if the tube is pressed into it when not in use. That also protects the tube from damage.
9. Sheet Seam can be cut using any sharp blade or small saw e.g. Stanley Knife. Make sure the cut has been thought about because it can’t be rejoined.
10. Damaged sections can simply be cut out and the remaining lengths used as two pieces. Overlap joins as explained before.
Correct at May 2022
Contact for orders or any problems CDavidLanceSilage@gmail.com